Special content
A chronicle of castings
Casting – a material-processing technique appreciated the world over – can be found here: 5,600 years of casting history
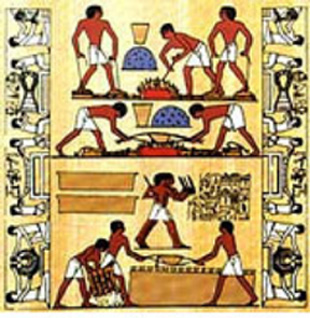
The first encounter between people and metals occurred between 5000 and 6000 BCE when natural gold, silver, and bronze were hammered into various shaped objects. Forging came to be the first method by which metals were actively processed. Come to think of it, Japanese swords are considered to be the result of the most advanced forging technique the world has ever known. The casting technique whereby metal is melted, poured into a casting mold, and then allowed to solidify began to be practiced in Mesopotamia around 3600 BCE, approximately 5,600 years ago. It all started when someone chose to melt bronze and pour it into a mold.
Egyptian papyruses from around 1500 BCE depict scenes of foot-operated bellows designed to send blasts of air into forges. The invention of the bellows enabled humankind to reach and maintain higher temperatures and helped usher in the Bronze Age. Incidentally, the melting point of bronze comprising 75 percent copper and 25 percent tin is approximately 800 degrees centigrade. For casting purposes, it is conceivable that melting temperatures exceeded 1,000 degrees centigrade in ancient times. In thinking about bronze ware, it is a bit of a mystery as to how someone came up with the notion of adding tin to the mixture. Tin was apparently sourced from eastern Iran (the Caucasus or Turkmen region), such that the person who originally conceived of this combination must have been some kind of genius.
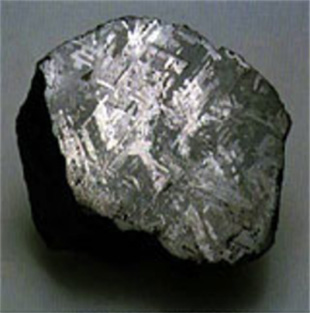
It is likely that the first time people came into contact with iron was through the discovery of iron contained in meteorites. Forging is possible thanks to the presence of significant amounts of nickel in meteorites. Meteorites feature a pattern known as the Widmanstätten pattern, which forms through gradual cooling at very slow speeds over millions of years. Iron-ring necklaces made from meteorites in around 3000 BCE have been found in Egypt.
Since iron on Earth oxidizes, it cannot be used as iron unless it is deoxidized. Iron was first obtained from the deoxidation of iron ore in the Hittite Empire in 1700 BCE Batch-type furnaces were apparently used to deoxidize iron sand with charcoal to extract spongy near-pure iron deposited on the bottom of each furnace. It appears that iron objects were obtained by heating and forging this iron. In an epic poem by Homer in around 800 BCE, iron is described as something that is extremely expensive. It is likely that iron was far more expensive than gold.
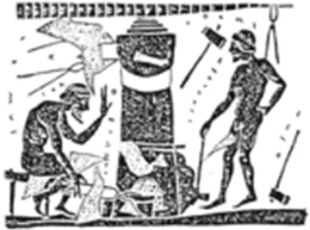
Since Homer also alludes to blacksmiths, it is believed that a hardening process had also been perfected during the era in which Homer was alive. Strangely enough, iron was produced in Europe by a forging process until the fourteenth century. Casting by melting iron and pouring it into casting molds did not take place on that continent until the fourteenth century. That knives and sabers were European weapons can perhaps be attributed to this difference in the history of iron. The casting technique whereby melted iron is poured into casting molds was first developed in China in around the seventh century BCE. It is believed that practitioners of bronze ware techniques in China managed to achieve considerably high temperatures with the use of bellows. This technique was likely adapted for the development of pig iron produced by melting high-carbon iron.
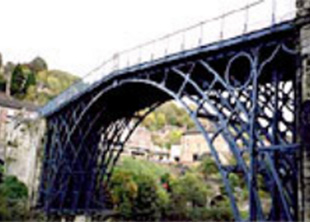
(Iron Bridge), England
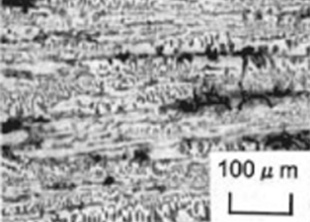
Since high-carbon iron has a relatively low melting point of approximately 1,150 degrees centigrade and is highly fluid in its molten form, the casting of iron was made possible. Chinese castings from around the fourth century BCE have compositions that are approximately as follows: carbon between 2.5 and 4.3 percent, silicon between 0.1 and 0.2 percent, manganese between 0.01 and 0.2 percent, phosphorus between 0.1 and 0.5 percent, and sulfur between 0.01 and 0.1 percent. Since castings with these compositions have low amounts of silicon, their structure is described as being chilled and is characterized as hard and brittle due to an absence of graphite.
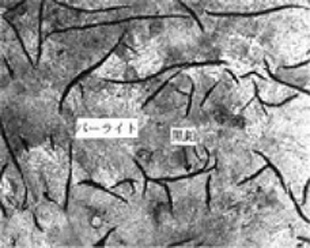
That no iron-casting technologies were transmitted to Europe until the fourteenth century could perhaps be attributed to this brittleness. It became possible to produce high-silicon cast iron without a chilled structure around the time the Iron Bridge was constructed in England in 1779.
Iron Bridge (made of cast iron), England Between the seventh century BCE and the advent of the Industrial Age in the eighteenth century, cast iron was hard and brittle. Thus, it makes sense that the iron in forged items that are tough and that can be rendered hard was highly appreciated. The quality of cast iron was changed to a ground-breaking extent by the addition of greater amounts of silicon. Cast iron that did not become chilled came to constitute an important material underpinning industry. The world began to churn out a host of different cast products, including bridges and cannons.
Modern cast iron benefited from two significant inventions. The first is the method by which high-strength flake graphite cast iron is manufactured based primarily on the inoculation technique devised by inventors G. F. Meehan and O. Smalley in the 1940s. This technique allows high-strength cast iron with a tensile strength of at least 300 N per square millimeter to be created on a stable basis.
The second is the existence of spheroidal graphite cast iron as discovered by Morrogh in England in 1947. This discovery made it possible to manufacture cast iron with strength of at least 800 N per square millimeter. This means that cast iron technology was evolving significantly at around the time of the end of the war in Japan in 1945. Japan adopted technologies from various countries in the post-war era and upgraded them to establish world-class casting technologies. No doubt, Japanese casting technologies will continue to improve by leaps and bounds in line with breakthroughs in the automotive industry.