Quality control
We are implementing a quality-first approach in order to produce better castings.
Implementing the quality-first (QF) approach: seeking to achieve a zero-defects goal
In order to produce better castings, we will make further improvements in quality.
Since our founding, we have been ceaselessly engaged in efforts to improve quality. We were granted ISO 9002 certification on March 16, 2001, and are presently carrying out quality-control measures based on ISO 9001 at all of our plants. We endeavor daily to improve quality in terms of full mold technology and DMP technology.
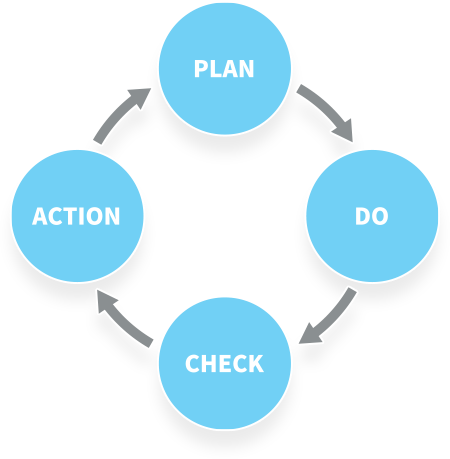
Quality-assurance system
In order to fully satisfy the varied demands of our clients, we carry out a thorough regimen of quality control. The demands of a client are incorporated into manufacturing procedures and deployed into manufacturing processes by engineering staff members in each section. Products are brought to life in line with client demands by trained on-site staff members.
Final shipping inspections are conducted by inspectors in the Quality Assurance Division, a section that operates at arms’ length from the Manufacturing Unit. Products that successfully pass a strict inspection will be delivered to clients.
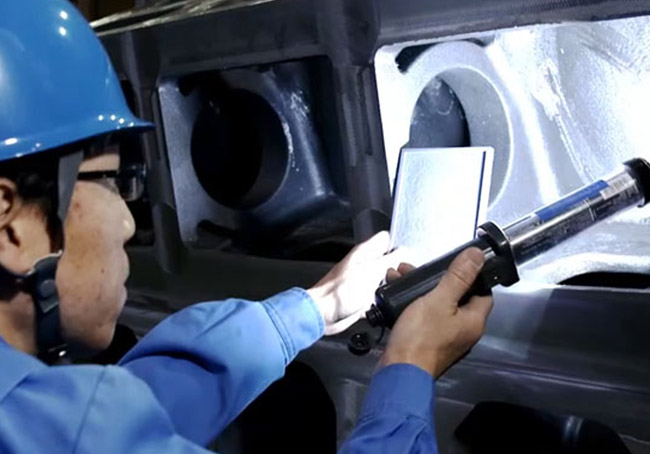
Main types of product inspections
<Material inspections>
Tensile testing (universal testing machine), impact testing (Charpy impact testing machine), hardness testing (Brinell hardness tester, portable hardness meter), metallographic examinations (optical microscope, SEM, EDS)
<Dimensional inspections>
3D dimensional measurements (ATOS, automated laser measuring instrument)
<Non-destructive inspections>
UT (ultrasonic testing), MT (magnetic testing), PT (penetrant testing),
ET (eddy-current testing), ST (stress-gauge testing), VT (visual testing)
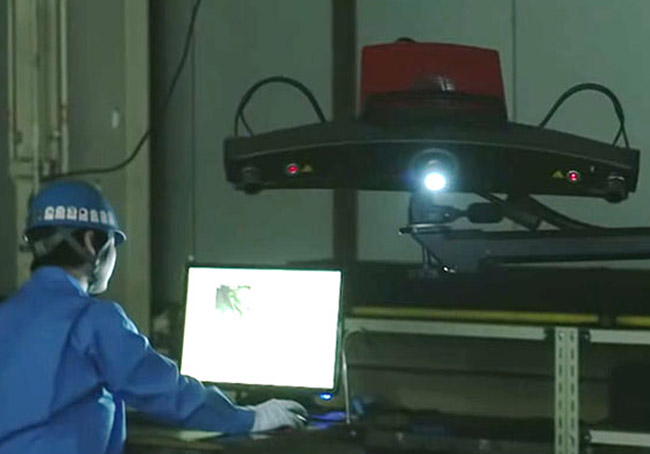
Creating a culture of improvements
At Kimura, we have cultivated a culture in which all employees are encouraged to submit improvement proposals every month. Awards are conferred by the heads of each unit during semi-annual enhancement months. Employees who submit the most exceptional improvement proposals over the course of a year win the President’s Award. The culture is such that sessions at which improvement reports are issued are regularly held and exceptional improvement reports can be shared with other units.
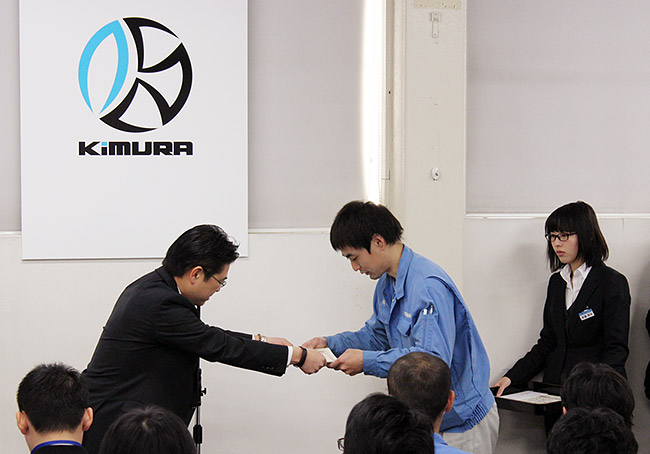
Support of the Development Division
In addition to conducting research and development work on the quality of materials and coatings and managing casting plans and casting sand, the Development Division provides on-site support in terms of IoT technology and various other elements. Whenever a defect or failure arises, the causes of such a failure are also analyzed with highly developed equipment. Activities to help spread knowledge concerning casting technology across the entire workforce of the company are being undertaken by having quality workshops for engineering staff members in other units held by members of the Development Division who possess specialized knowledge.
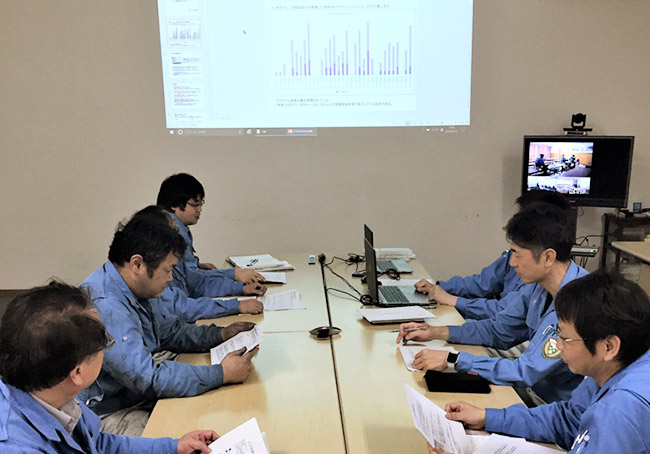
Education and training
We promote correspondence courses as a form of education and training designed to raise the skill levels of our employees. Each year, many employees take these courses for self-development purposes. In addition, we strive to enable our employees to obtain qualifications by urging them to proactively participate in internal workshops and outside courses and academic conferences. Each unit also provides special training sessions. All of these various initiatives are managed with the use of skill charts that are maintained as individual records for each employee.
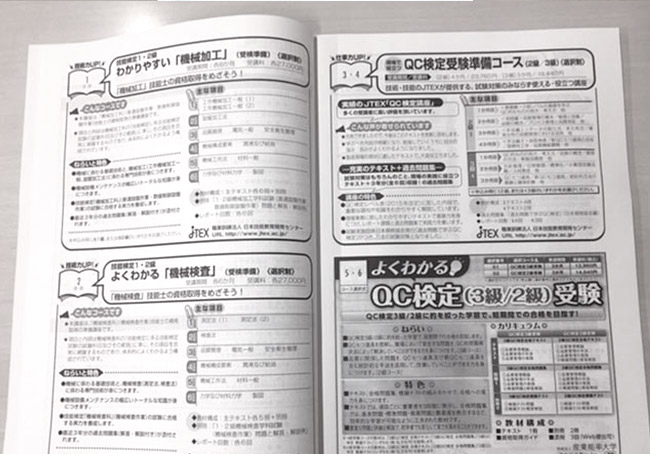
Certifications and qualifications
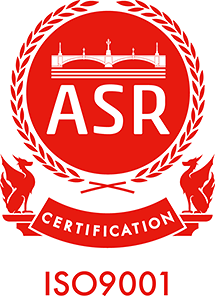
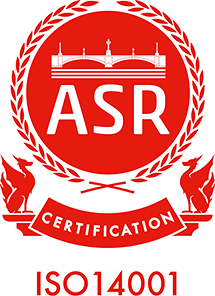
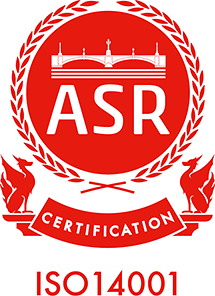
Vessel classifications
Nippon Kaiji Kyokai <ClassNK>
Castings requiring the approval of Nippon Kaiji Kyokai can be manufactured.
Omaezaki Plant, Kimura Foundry Co., Ltd.: Grey & Ductile
Cast Iron
Gunma Plant, Kimura Foundry Co., Ltd.: Grey & Ductile
Lloyd's Register <LR>
Castings requiring the approval of Lloyd’s Register can be manufactured.
Omaezaki Plant, Kimura Foundry Co., Ltd.: Grey & Ductile Cast Iron (Max.35 ton)
Gunma Plant, Kimura Foundry Co., Ltd.: Grey Cast Iron (Max.7 ton)
DNV GL
The result of a merger between Det Norske Veritas (Norway) and Germanischer Lloyd (Germany) in September 2013.
Castings requiring approval for the above vessel classifications can be manufactured.
Gunma Plant, Kimura Foundry Co., Ltd.: Grey & Ductile Cast Iron (Max.7 ton)
American Bureau of Shipping <ABS>
Castings requiring the approval of the American Bureau of Shipping can be manufactured.
Omaezaki Plant, Kimura Foundry Co., Ltd.: Grey & Ductile Cast Iron (Max.30 ton)
Gunma Plant, Kimura Foundry Co., Ltd.: Grey & Ductile Cast Iron (Max.12 ton)
CHINA CLASSIFICATION SOCIETY <CSS>
maezaki Plant, Kimura Foundry Co., Ltd.: Grey Cast Iron (Max.4.2 ton)
Nondestructive inspections
Certification organization: Japanese Society for Nondestructive Inspection (JSNDI)
UT (ultrasonic testing): Level 3 (3 persons)
MT (magnetic testing): Level 3 (2 persons)
PT (penetrant testing): Level 3 (5 persons)
RT (radiographic testing): Level 3 (1 person)
ET (eddy-current testing): Level 2 (1 person)
ST (stress-gauge testing): Level 3 (1 person)
Certification organization: American Society for Nondestructive Testing (ASNT)
UT (ultrasonic testing): ACCP Level 3 (2 persons)
MT (magnetic testing): ACCP Level 3 (2 persons)
PT (penetrant testing): ACCP Level 3 (1 person)
RT (radiographic testing): ACCP Level 3 (1 person)
VT (visual testing): ACCP Level 2 (3 persons)
*Possessed by multiple persons; highest level.
*In addition to certifications granted by outside certification organizations, internally certified qualifications that are in accordance with the SNT-TC-1A standard are also possessed.
(As of March 2022)
National Association of Corrosion Engineers (NACE)
Level 2 (3 persons)
*Possessed by multiple persons; highest level.
Welding management
Welding management engineer (JIS Z 3410) Grade 1 (1 person)
Welding technician (JIS Z 3801) N-1F (1 person), A-2F (5 persons), A-2V (1 person)
*Possessed by multiple persons; highest level.