Full Mold Casting
This casting method results in products created by displacing foamed patterns with molten metal.
Features of Full Mold Casting Process
- Faster start-up and delivery compared to the conventional wooden patterns;
- “Vertical start-ups” by a huge production capacity of milling foamed patterns.
- No storage nor repairing costs for wooden patterns.
- Easy geometrical validation before casting.
- More flexibility for updating and revising design.
- Size and weight range
- Maximum length: 8,200 mm
Maximum Weight: 44 tons
- Production
- 78,000 tons per year
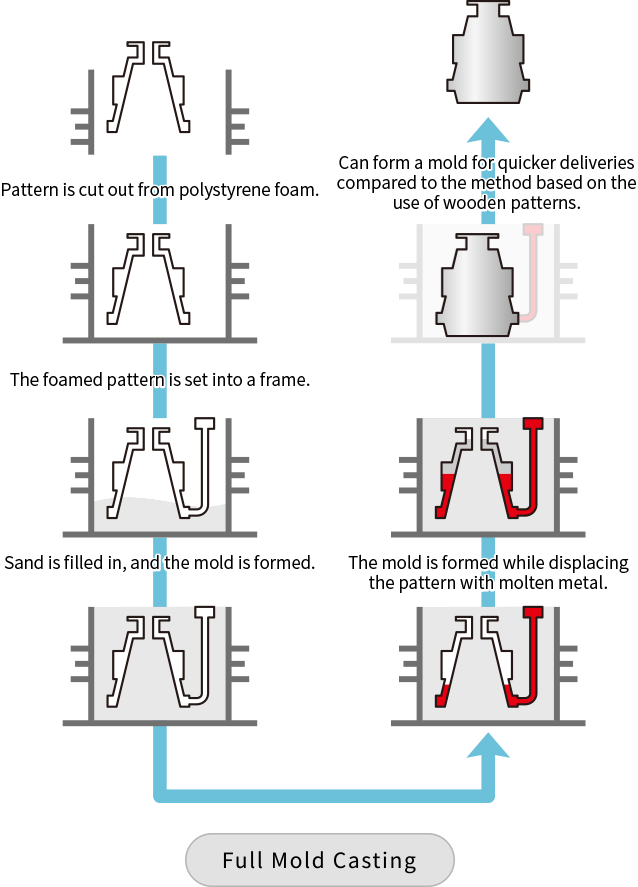
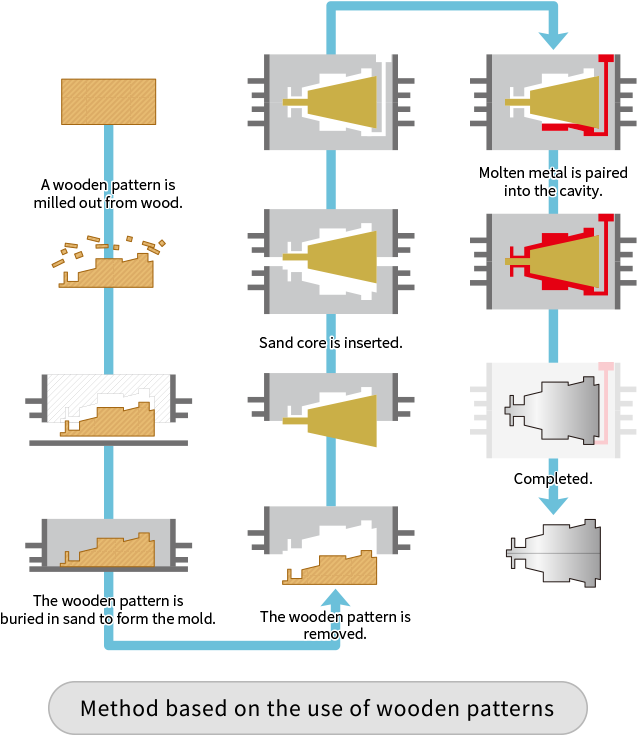
Differences between Full Mold Casting and conventional wooden patterns
The full mold casting process is a casting method frae replaces molded pattern by molten metal.
Since the casting mold is filled, with a pattern, this method is referred to as Full Mold Casting.
This name was given to highlight the contrast between this method and the cavity mold method whereby molten metal is poured into the cavity molded by wooden patterns.
The table blow shows a comparison between Full Mold Casting process and conventional wooden pattern process.
Advantages of the Full Mold Casting process and the wooden pattern method
Full Mold Casting process | Conventional wooden pattern process |
---|---|
Suitable especially for one shot production including prototypes and artistic casting with short lead-time. No wooden pattern fee required. | Suitable for serial production with wooden pattern fee. |
Good combination of CAD/CAM, 3D data, and material of formed pattern ; it is easier to work on the same shape of its real product and on formed pattern. |
Since a wooden pattern entails the creation of parts that are not taken up by the casting itself and since a wooden pattern is not as workable as polystyrene foam, 3D data and CAD/CAM technology cannot be easily utilized. |
Higher technology required as so called “carbon residue ” needs to be connected and rumored from the casting. | Most of all sand casting foundries share this standardized process. |
No storage required. | Storage and repairing fee for wooden pattern required. |
Visual pattern check available in front of completed foamed pattern. | More experience needed for wooden pattern validation. |
Higher flexibility for design with no sand cores needed. | Higher skills and longer time required for designing complex sand cores and casting plan. |
Lighter casting with no draft angle and less design limitation. | Draft angle always required. Limited design due to its process. |
History of the Full Mold Casting process
Origin of the name
The full mold casting process is known by a number of different names, including evaporative pattern casting, lost foam process, EPC process, and FMC process.
Full mold casting is a term that corresponds to cavity molds in the wooden pattern method, which is characterized by the presence of empty space inside casting molds.
History
The basic patent for the full mold casting process for which an application was submitted by American H.F. Shroyer was granted in 1958. The dry sand method was invented by H.B. Dieter and T.R. Smith in 1964. In 1967, A. Wittmoser and Hoffman of Germany came up with a magnetic method of casting.
A license for the basic patent for the full mold casting process was acquired by Gruenzweig & Hartmann (abbreviated as “G+H”), a German company that produced insulating materials, in 1961. Wittmoser of RWTH Aachen University, who had been appointed vice-president of this company, sought to commercialize this technology and spread it throughout the world. Wittmoser in essence became the father of the full mold casting process.
In Japan, Mitsubishi Yuka Badische Co., Ltd., acquired a patent license from Full Mold International, a company that was operated by Wittmoser, in around 1965, whereupon Mitsubishi Heavy Industries engaged in technological development. At one point, up to 120 companies belonged to a family of enterprises that carried out the full mold casting process. In November 1966, KIMURA as a company became a member of this family.
The full mold casting process of the time yielded such poor-quality products that only press dies for automobiles could make full use of its advantages. The sudden passing of Wittmoser, who had played a central role in popularizing the full mold casting process, in November 1993 caused the licensing group to discontinue operations, which in turn led companies to develop the process on their own. It is clear that the full mold casting process is carried out by chemical manufacturers of polystyrene foam for the purpose of expanding the range of products made with polystyrene foam. A worldwide debate unfolded to determine which method was better: the top-pouring casting approach endorsed by Wittmoser or the bottom-pouring casting approach endorsed by President Kimura. In 1980, the basic patent lapsed. Up to that point in time, the full mold casting process was primarily used for large castings, such as press dies. However, the full mold casting process subsequently came to be applied to smaller products, including non-conventionally shaped tubes and pipes and automotive parts.
General Motors applied full mold casting technology to its aluminum alloy cylinder heads in 1980 while Ford and Fiat did the same thing for the mass production of small articles in 1982 and 1984, respectively. These applications were primarily based on molding methods implemented with vibrating molding machines that utilized sand without binders. This technology is most commonly referred to as the lost foam process . At about the same time in Japan, the full mold casting process came to be adopted for the mass production of small articles to herald the arrival of a second boom for the full mold casting process.
For large-scale castings, the full mold casting process did not readily spread in terms of application beyond press dies because of the issue of residue (that remains after the polystyrene foam is burned), which is a noted shortcoming of this method. However, the full mold casting process, which does not require wooden patterns, is undoubtedly the ideal method for producing single-unit castings. We have been endeavoring to apply the full mold technology to machine tools and industrial machinery since 1974 and refer to this technology as the new-full mold casting process (“new-FMC” for short). Since this new-FMC technology was our own proprietary technology and since it was limited to single units, it was not capable of stimulating another boom.
In 1987, we adopted a method of producing full mold patterns based on the use of a CAD/CAM system. This opened up a new path for the mass production of castings. We ended up taking on the challenge of mass producing machine tools castings through the application of the full mold casting process. This technology evolved to accommodate composite castings of machine tools and industrial machinery.
The CAD/CAM system that was adopted for the full mold pattern making process in 1987 completely transformed the way in which patterns were subsequently created. Traditionally, a pattern was made by first imagining the space to be occupied by a product based on its two-dimensional drawing and then creating parts by using band saws and other tools and putting these parts together. In line with the evolution of computers, the process of making patterns by hand gave way to the process of making patterns with the use of CAD/CAM systems. By 2002, we no longer made patterns by hand. This revolution in the process of making patterns opened up a viable path towards the mass production of full mold castings.
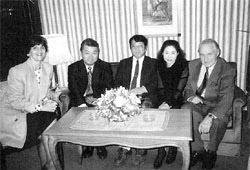
(Taken at hotel on the outskirts of Mainz eity October 1993)
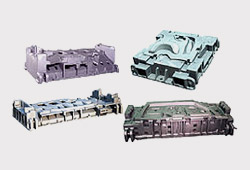
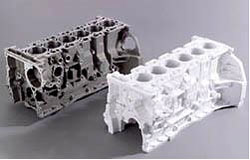
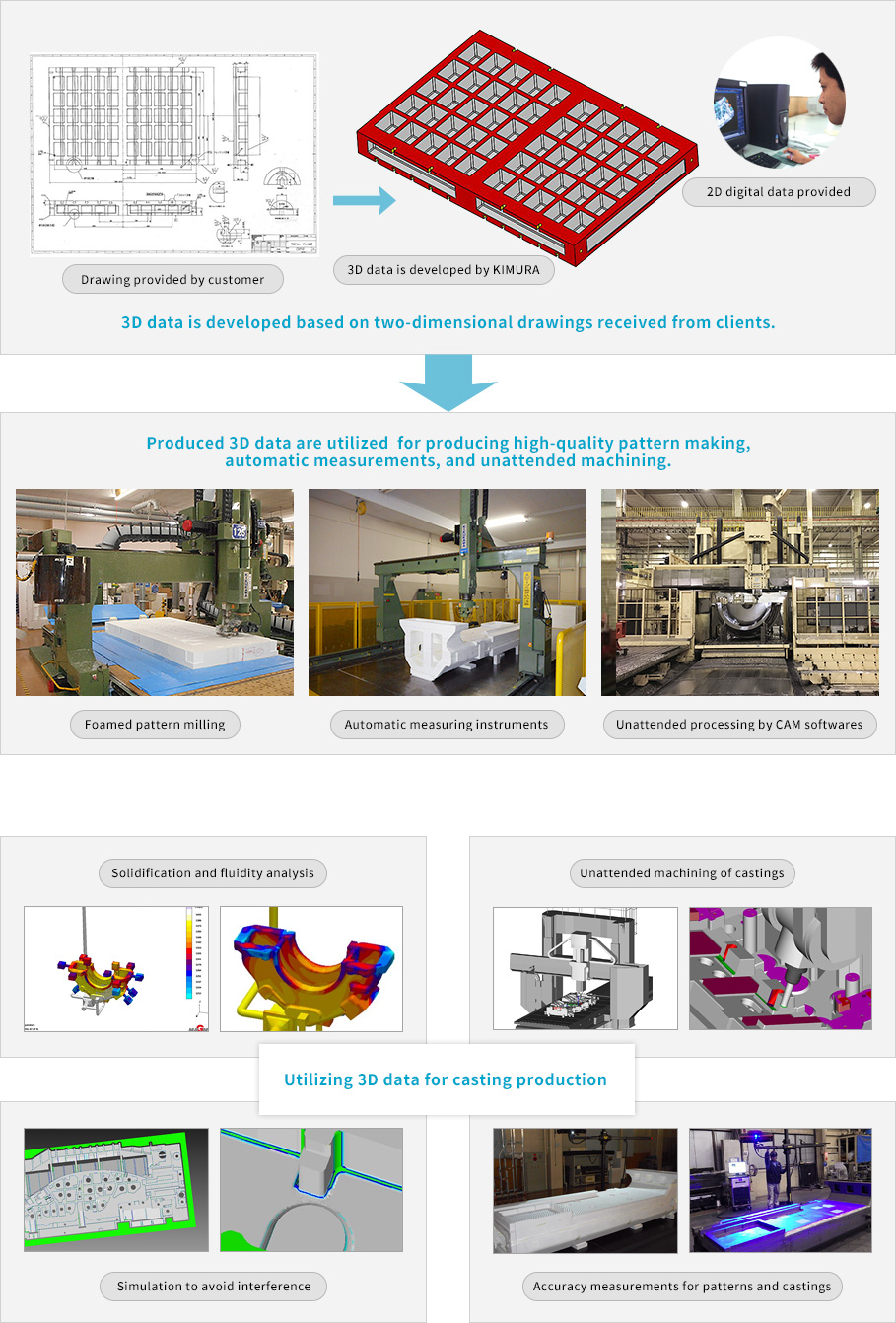
Landscape castings produced by Full Mold Casting technology
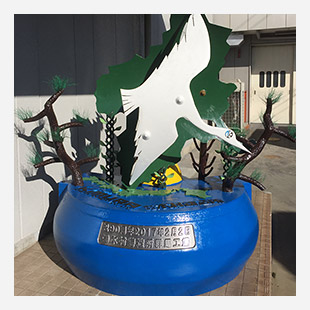
90th anniversary (Gunma Plant)
Gunma Prefecture in the Shape of a Dancing Crane
Dimensions: 1748 x 1333 x 2080
Weight: 2060 kg
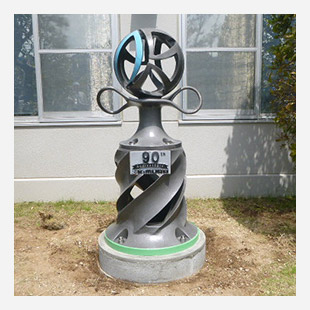
90th anniversary (Head Office Plant)
Infinite Possibilities
Dimensions: 740 x 700 x 1500
Weight: 716 kg
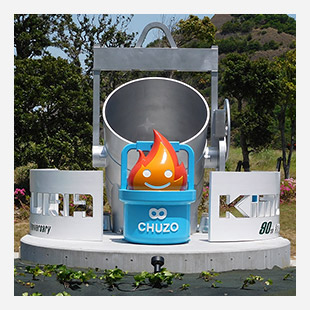
90th anniversary (Omaezaki Plant)
Chuzo-kun
Dimensions: 2493 x 2088 x 3394
Weight: 5680 kg
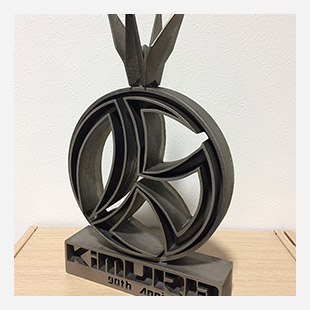
90th anniversary (Advanced Process Technology Center)
Orizuru
Dimensions: 340 x 210 x 100
Weight: 8 kg
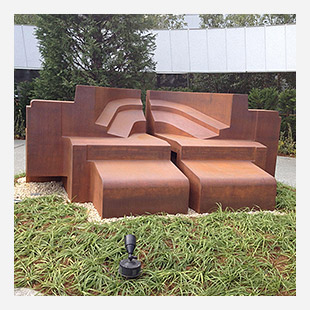
Topos (site) Reproduction
(PARK HABIO Shinjuku East Side Tower)
Dimensions: 3380 x 2300 x 1520
Weight: 7750 kg
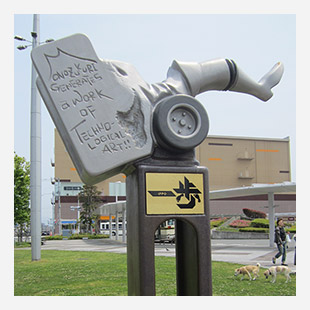
39th World Skills Competition 2007
(Numazu Station North Exit)
Ippo
Dimensions: 900 x 500 x 1800
Weight: 1200 kg
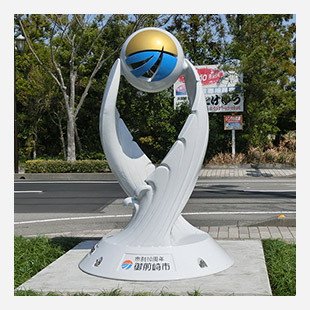
Omaezaki City Hall – to celebrate the 10th anniversary of the granting of city status
Dimensions: 1300 x 1300 x 1800
Weight: 2380 kg
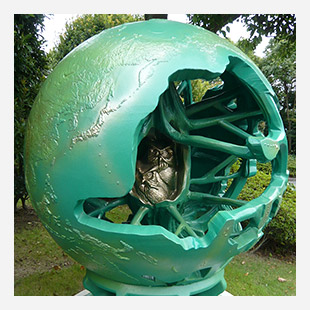
Japan Manufacturing World 2007
Exhibition commemoration (National Museum of Nature and Science)
Wise Owl
Dimensions: 1700 x 1700 x 2000
Weight: 6700 kg
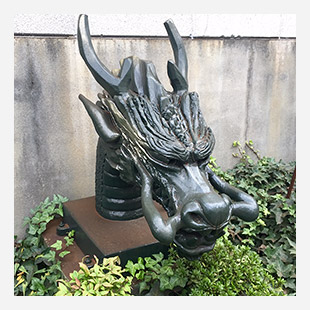
Dragon’s Head(Winner of the 1st Manufacturing Contest Incentive Awards as hosted by the Sokeizai Center; Head Office Plant)
Dimensions: 350 x 800 x 900
Weight: 800 kg
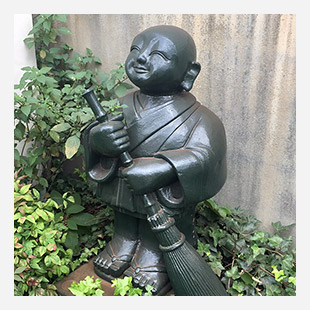
Young Cleaning Monk (Head Office Plant)
Dimensions: 400 x 350 x 900
Weight: 600 kg
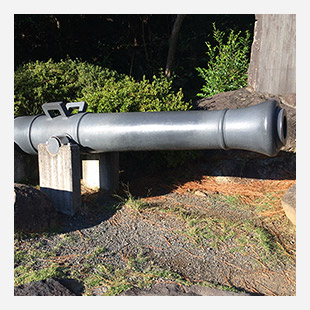
24-pound cast-iron cannon at the Nirayama Reverberatory Furnace(reconstructed based on archival documents)
Dimensions: 3500 x 500 x 500
Weight: 3500 kg
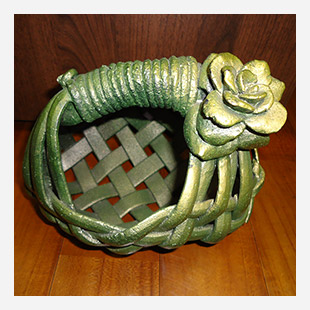
Flower Basket
(Reproduction of the possibilities inherent in the full mold casting process)
Dimensions: 250 x 200 x 180
Weight: 4 kg