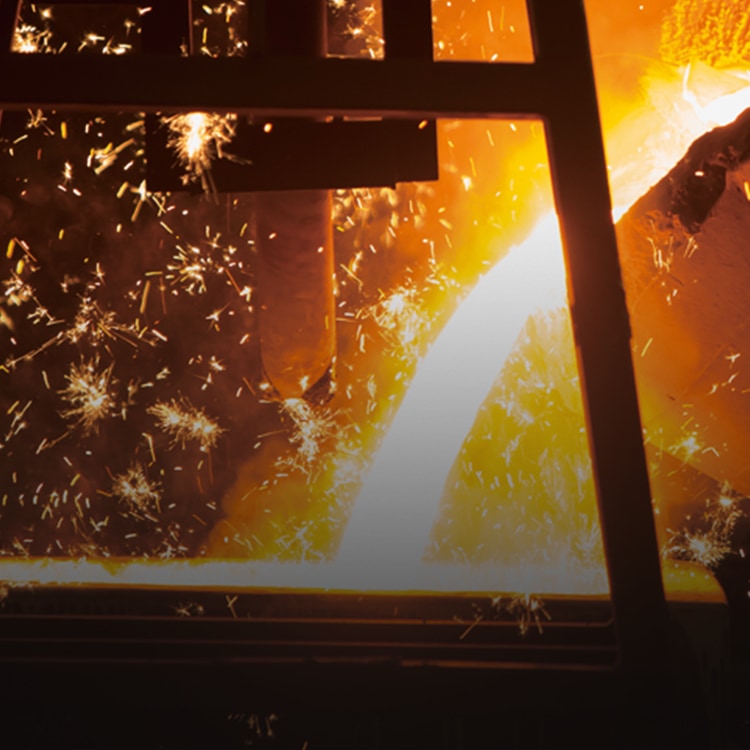
フルモールド鋳造法
発泡スチロール模型が溶湯に置換され、
製品となる鋳造法です。
鋳造とは?鋳物とは?木村鋳造所の鋳物製法「フルモールド鋳造法」の魅力とは?
鋳物(いもの)を造ると書いて鋳造(ちゅうぞう)と言いうことから分かる通り、鋳造で出来た物を鋳物と呼びます。鋳物とは金属を溶かして型に流し、冷やし固めて作る金属製品のことです。鋳造の技術を利用して製造される鋳物は多くの産業を支えています。そして古い金属を溶かして新しい鋳物を造る鋳造は古くから続く循環型(リサイクル)の産業です。
さまざまな工法があるなかで木村鋳造所は、フルモールド鋳造法をメインに鋳物を製造しています。フルモールド鋳造法の最大の魅力は「短納期」です。特に、開発品や試作品の鋳物の場合に工期と費用を大きく短縮することができます。お客様の図面や3Dデータをお預かりして発泡スチロールの模型(鋳型)を製作し、鋳物を造ります。図面から3Dデータを製作することも可能です。鋳型(いがた)とは鋳物の型で、フルモールド鋳造法で言えば発泡スチロールの模型です。
なお、ねずみ鋳鉄(FC)とダクタイル鋳鉄(FCD)は最大40トンまで、鋳鋼は3トンまで対応しております。
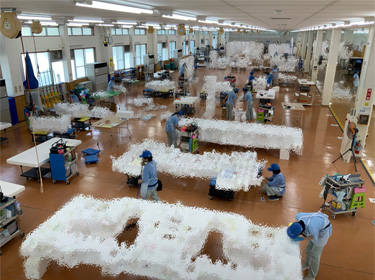
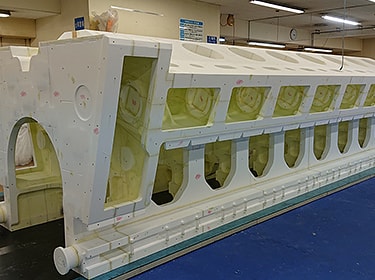
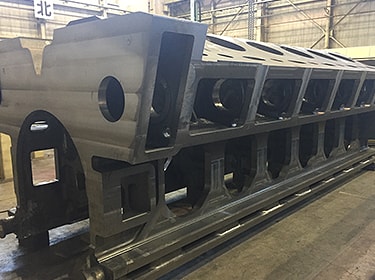
製品事例
木村鋳造所がフルモールド鋳造法で製造している鋳造品は、大きく分けて「自動車ボディプレス金型用鋳物」、「工作機械部品用鋳物」、「産業機械部品用鋳物」の3つです。
自動車ボディプレス金型用鋳物
自動車のボディを成型するための「プレス金型」は、一般的に鋳鉄製の鋳物で作られています。これらの鋳物は、ブランキング、ドロー、トリム、ピアス(リスト・フランジ・ベンドなど)などといったボディプレス各工程の金型の素材として使用されます。
木村鋳造所では長さ8.6mの鋳枠を保有しており、ボディサイドアウター(サイドパネルアウター・サイドメンバー)、ドアフロント・ドアリア、フードのそれぞれアウター・インナーのセット取りなど大物金型用鋳物に対応できる設備を揃えています。
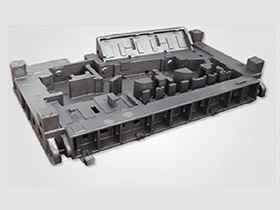
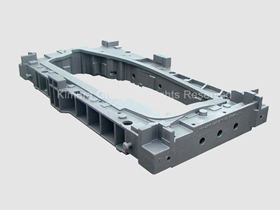
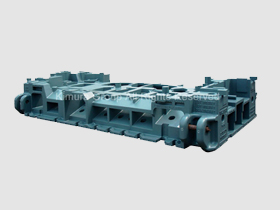
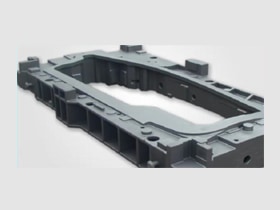
自動車ボディプレス金型用鋳物Kimuraの強み。
- 安定した品質
「短納期」対応はもちろんですが、安定した「高品質」が強みです。自動車ボディプレス金型用鋳物は、一般的にフルモールド鋳造法で製造されていますが、発泡模型製造までを内製化している会社は多くありません。内製化により、発泡模型から鋳物まで一貫した納期および品質管理を実現しています。さまざまな製品検査を行っておりますのでご希望がございましたら、お問い合わせください。 - さまざまな材質に対応
材質は、鋳鉄を中心にJIS(FC250、FC300、FCD550、FCD700など)に代表される国内材質のみならず、DIN(GG25、GG30、GGG500、GGG700など)やEN(GJL-250、GJL-300、GJS-500、GJS-700など)などの海外材質にも対応可能です。もちろん、独自の材質要求や鋳鉄以外の鋳鋼材質(3トン未満)も対応可能です。パッド、パンチ、刃材(セクショナル・ダイ)などの受注実績があります。材質についてのご質問がございましたらお気軽にお問い合わせください。 - 豊富な実績
ボディサイドアウター(BSO・サイドメンバー・サイドパネル)、ドアフロント・ドアリア、フードのそれぞれアウター・インナーなど大物金型用鋳物だけでなく、フェンダー、ルーフ、バックドアアウター・インナー、トランクリッド、バンパー、ホイールハウス、フロアなど、あらゆるボディプレス金型パネルに対応することができます。また、ボディプレス金型用鋳物以外にもダイキャスト型用鋳物や射出成型型(バンパー型)用の取付板などの製造実績があります。
工作機械部品用鋳物
マシニングセンタをはじめ旋盤(ターニング)、研削盤、各種門形・立形・横形加工機、放電加工機、歯切り盤など、各種工作機械向けに、ベース、ベッド、フレーム、テーブル、コラム(キャレッジ)、サドル、スピンドルヘッドなど様々な部品を製造・供給しています。また、治具としてイケールや定盤の製造実績もあります。ねずみ鋳鉄(FC)が中心ですが、ダクタイル鋳鉄(FCD)での製造も可能です。ボディプレス金型用鋳物と同様に短納期かつ高品質の鋳物をお客様のご要望に合わせて供給しています。
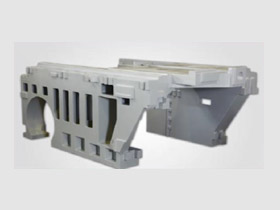
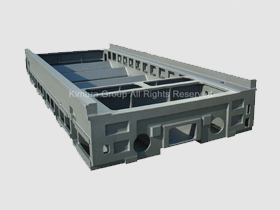
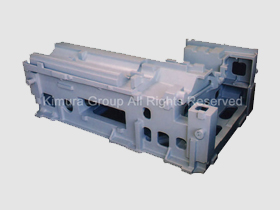
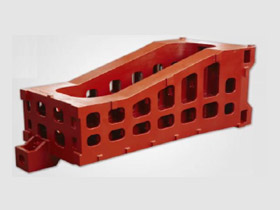
工作機械鋳物Kimuraの強み。
- 型(木型)の製作・管理が不要
フルモールド鋳造法では、3Dデータを元に発泡模型を削り出しますので、鋳型(木型)の製作や保管するための倉庫を準備する必要もありません。ご要望に応じて、3Dデータは弊社で責任を持って保管いたします。 - 「垂直立ち上げ」に対応→開発から量産への移行をイメージさせる柔軟性
短期間で複数個の需要が発生した場合(「垂直立ち上げ」)にも、弊社のフルモールド鋳造法は非常に便利です。発泡模型を削り出す専用加工機を40台以上保有していますので、一つの3Dデータから同時に複数個の発泡模型を削り出すことが可能です。また、この模型切削能力は垂直立ち上げだけではなく、量産対応も可能にしています。 - あらゆる製品サイズに対応
最大長さ8.6mの鋳枠を保有し最大40トンの製品重量まで製造できる設備を備えており、「大物」部品の製造に対応しております。また、製品重量1トンを下回るような部品の場合は、当社のダイレクトモールディングプロセス(DMP)法もしくは、フルモールド鋳造法・小物鋳物を得意とする協力メーカーで、柔軟に対応させていただいております。
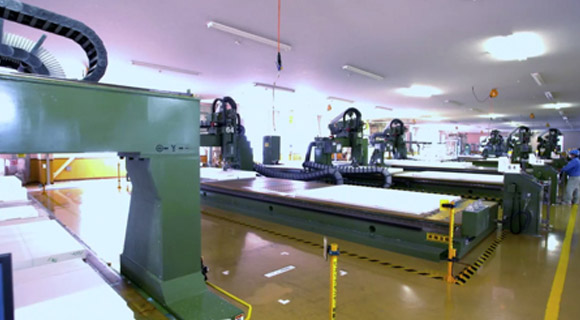
弊社保有鋳枠サイズ(一部) |
---|
8,600x3,800mm |
6,400x4,300mm |
5,300x3,000mm |
4,500x2,800mm |
産業機械部品用鋳物
プラスチック製品や液晶パネルなどの自動車・電気製品製造装置や発電、風力発電、上下水道、ゴミ処理施設、石油採掘、化学工場、船舶などで使用される大型設備にも木村鋳造所の鋳物が使用されています。
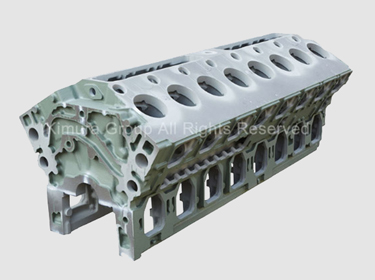
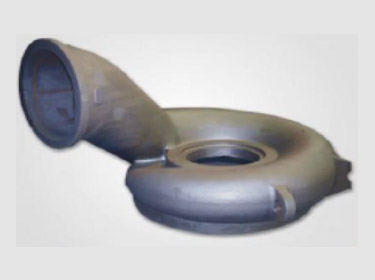
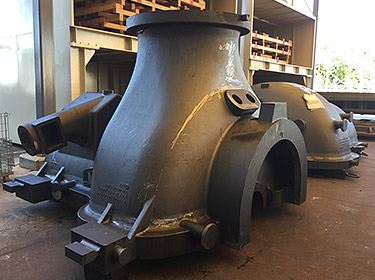
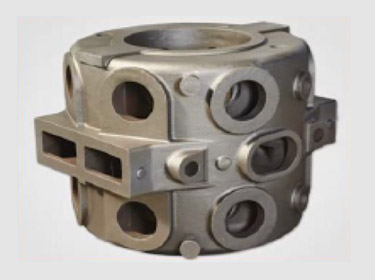
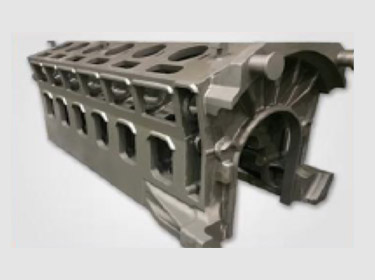
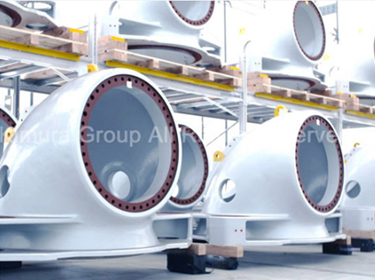
EN-GJS400-18LT 2,350kg
産業機械用鋳物Kimuraの強み。
- 毎回設計・仕様が変わる工業製品や、開発・試作品に最適
ポンプやコンプレッサーなどは、設置される工場やプラントの制約条件に合わせた設計や仕様が必要となります。フルモールド鋳造法では、短納期かつ低初期費用で高品質の鋳鉄部品を供給することができます。また、ディーゼル・ガスエンジン用のシリンダブロック(架構・クランクケース)やガスタービンケーシングなどは、性能試験前に型(木型)を製作してしまうと、性能向上のための設計変更が限定されてしまう可能性があります。フルモールド鋳造法の場合は、元となる3Dデータを修正するだけで発泡模型を削り出し、鋳物を製造することができます。 - 数々の部品製造実績
産業機械であれば、射出成型機、プレス機、圧造機、レーザー加工機、液晶露光装置、印刷機、ミキサー、変速機(ギアボックス)などの部品を製造してきた実績があります。また、産業設備向けには、ポンプケーシング、インペラ、送風機(ブロワー)、ガスエンジン、ディーゼルエンジン、ガスタービン、風力発電部品(陸上・洋上)、風車部品(陸上・洋上)、コンプレッサーケーシング、ダイアフラム、旋回機(スラスター)などの部品を多数供給しております。お客様のご要望に合わせて、鋳造設計についても柔軟にご相談させていただきます。 - 幅広い材質に加えて、素材検査、塗装、加工まで「ワンストップサービス」で対応
フルモールド鋳造法の特徴として、従来のねずみ鋳鉄(FC)、ダクタイル鋳鉄(FCD)にとどまらず、3トンまでであれば鋳鋼材質にも対応可能です。社内に機械的性質試験設備(引張試験・衝撃試験)を備えており独自材質の開発も行っているため、お客様のご要望に幅広くお応えすることができます。また、目視検査(VT)だけでなく、浸透探傷検査(PT)、磁粉探傷検査(MT)、超音波検査(UT)などの各種非破壊検査資格を持つ検査員を有しており、品質を維持・向上する能力を備えています。さらに、お客様のご要望に応じて塗装や切削加工も請け負っており、模型製作から完加工までをワンストップサービスで供給することが可能です。
木村鋳造所のフルモールド鋳造法製造能力
発泡スチロール模型製造・鋳造・切削加工能力
木村鋳造所が有する、各工程・工場の製造能力は、以下の通りです。
模型工場
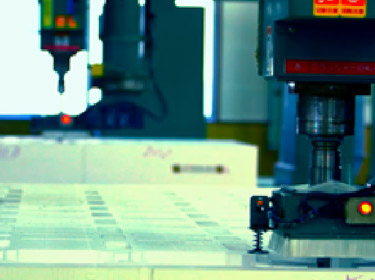
伊豆模型工場 | 2,000t/月 |
群馬模型工場 | 2,500t/月 |
御前崎模型工場 | 2,000t/月 |
月産能力合計 6,500t/月 | |
人員:250名 |
鋳造工場
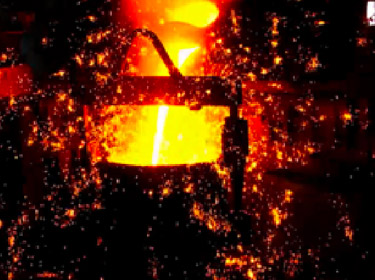
群馬鋳造工場 | 1,500t/月 |
御前崎鋳造工場 | 4,500t/月 |
月産能力合計 6,000t/月 | |
人員:400名 |
加工工場
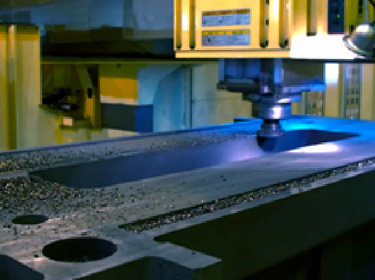
門型5面加工機 | 11台 |
縦旋盤台 | 2台 |
固定5軸機 | 1台 |
5軸制御縦型MC | 3台 |
複合旋盤機 | 1台 |
横中ぐり加工機 | 1台 |
人員:50名 |
材質・サイズ
木村鋳造所のフルモールド鋳造法では、ねずみ鋳鉄(FC)、ダクタイル鋳鉄(FCD)にとどまらず、3トンまでであれば鋳鋼材質にも対応可能です。また、独自の材質も開発しており、お客様のご要望に合わせて材質を調整することも可能です。
KSCD-800I
用途:プレス金型 / 耐摩耗用部品
特徴:KSCD-800Iは自動車用薄板鋼材の加工硬化特性を鋳鉄に応用した耐摩耗材料です。プレス成型時の摩擦で硬化が起こりますので、繰り返し使っても摩耗しにくい素材となっております。顕微鏡組織は伸びのあるフェライト・パーライト混合組織にしておりますので、一般的な合金鋳鉄に比べて溶接性が良好です。また合金鋳鉄であるため、良好なフレームハード性を有しています。なお、フレームハード後クロムメッキを行う場合、水素脆性により割れが発生することがありますので、クロムメッキを行う場合は、KSCD-700IもしくはKSCD-800ISをご使用下さい。本材質は海外及び国内メーカーですでに使われており、その実力は実証済みです。
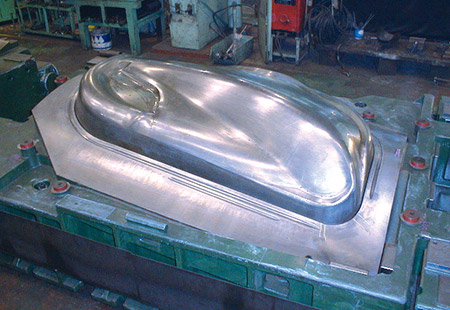
KSCD-800IS
用途:プレス金型 / 切刃・曲刃
特徴:強度の高いパーライト組織と伸びのあるフェライト組織を混合させることで、高強度と高い衝撃特性を両立させることに成功しました。本材質も合金を含むため、フレームハード性は良好です。またフェライト組織を含むため、一般的な合金鋳鉄に比べて溶接性が良好です。また衝撃値を低下させる不純物元素を極限まで下げることにより「刃こぼれ」をなくしました。こちらの材質も海外及び国内で長年の実績があり、広くご使用いただいております。
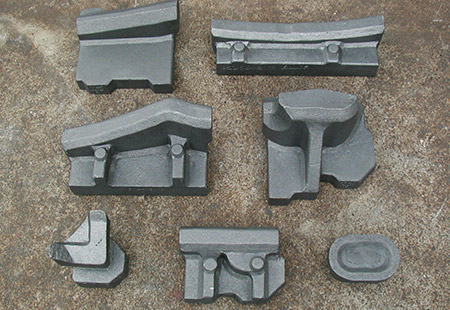
KMD-800Kシリーズ
用途:肉厚鋳物 / ダイキャスト金型の固定型
特徴:KMD-800Kは高強度のパーライト基地鋳鉄でありながらも引け巣を抑制した新素材です。ひけ巣でお困りの製品にぜひお試し下さい。また、黒鉛の微細化処理を行っておりますので、従来の鋳鉄より良好な面粗度が得られます。用途に応じて強度を調整することも可能です。
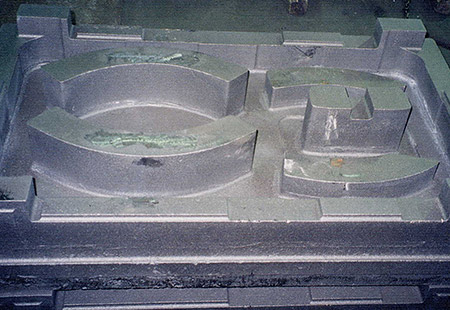
NS-FC300
用途:肉厚鋳物 / 定盤
特徴:NS-FC300はひけ巣を防止したねずみ鋳鉄です。定盤や肉厚製品など、ひけ巣でお困りの製品にぜひお試し下さい。
また面粗度品質を改善したグレードも準備しておりますので、定盤などで高い面粗度品質を必要とされる場合にはご相談ください。
Nobi-duc
用途:ダイキャスト金型・プレス機械・産業機械等の構造用部品
特徴:Nobi-duc(ノビダク)は表面にフェライト層を有する2層構造です。表面のフェライト層と内部の高強度・高靭性特性の組み合わせにより、高い破壊靭性を持つため、大きな負荷がかかっても変形や破壊が起こりにくい材質となっています。鋳鋼に匹敵する機械的性質を有するため、鋳鋼から鋳鉄への代替を可能とする新素材鋳鉄です。
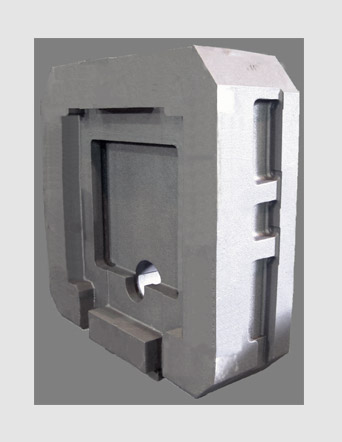
INJ400
用途:樹脂成形型
特徴:樹脂成型用の金型は、主として鍛鋼のブロックを加工して作られてきました。しかしながら、鍛鋼には歩留まりが悪く、加工時間が長いという問題がありました。これを解決するため、ニアネットシェイプの鋳鉄品を使うという試みがなされてきましたが、黒鉛の凹み等が樹脂に転写される問題があり、なかなか実現できませんでした。INJ400は、黒鉛を細かくして樹脂に転写されないようにした、樹脂成形型専用の球状黒鉛鋳鉄です。鋳造品なので、加工工数と歩留まりを鍛鋼より大幅に低減させることができ、低コスト化や短納期化を進めることができる材料です。
KIMS60
KIMS60は、JIS規格の合金工具鋼であるSKD11を鋳鋼に置き換えたニアネットシェイプな材料です。焼入れ〜焼戻しによる硬度特性はSKD11と同じですが、成分調整と熱処理の組み合わせによって、炭化物の分散と基地パーライト組織の粒状化が図られており、溶接時の割れ発生が抑えられています。またKIMS60は鍛造による組織の方向性もないため、鍛造方向による変形の差などもありません。SKD11と比べて、より扱い易い材質となっています。
フルモールド鋳造法とは?
材質ごとの一般的な鋳造方法とフルモールド鋳造法
フルモールド鋳造法をより理解していただくために、まずは、鋳鉄・鋳鋼で用いられる他の鋳造法との比較や、他の材質との比較をしてみました。
鋳鉄・鋳鋼
鋳造方法 | 製品事例 | ||
---|---|---|---|
|
|||
木型鋳造法 型(木型)を作製し、その型を用いて鋳型を作ります。 ・生型 ・自硬型 ・シェル型 ・Vプロセス(鋳型減圧鋳造法) |
シリンダブロック、シリンダヘッド、カムシャフト、オイルポンプハウジング、ブレーキロータ、デフケース、ブレーキキャリパ、インテークマニフォールド、船舶用・発電用クランクケース、歯車箱、軸箱、バルブボディ、旋盤ベッド、マシニングセンターコラム、歯車減速機ケース、圧縮機スパイラルケーシング、コンプレッサーダイアフラム、ガスタービンケーシング、ディーゼルエンジンシリンダブロック | ||
フルモールド鋳造法(消失模型鋳造法) 発泡スチロール模型を作製し、それを砂に埋めて鋳型を作ります。 |
自動車ボディプレス金型用鋳物、 工作機械部品用鋳物(ベース、ベッド、フレーム、テーブル、コラム(キャレッジ)、サドル、スピンドルヘッドなど)、 シリンダブロック、シリンダヘッド、カムシャフト、オイルポンプハウジング、ブレーキロータ、デフケース、ブレーキキャリパ、インテークマニフォールド、風力発電用鋳物、船舶用・発電用クランクケース、歯車箱、軸箱、バルブボディ、旋盤ベッド、マシニングセンターコラム、歯車減速機ケース、圧縮機スパイラルケーシング、コンプレッサーダイアフラム、ガスタービンケーシング、ディーゼルエンジンシリンダブロック、 景観鋳物 | ||
ダイレクトモールディングプロセス(DMP) 砂型を3Dプリンタで直接積層して鋳型を作ります。 同工法の鋳鉄・鋳鋼材質への適用は、木村鋳造所が実現しました。 |
シリンダブロック、シリンダヘッド、シリンダブロック、シリンダヘッド、オイルポンプハウジング、ブレーキキャリパ、インテークマニホールド、バルブボディ、タービンハウジング、ベアリングハウジング、油圧バルブ部品、ナックル | ||
|
ナックルステアリング、オーディオインシュレータなど | ||
|
シリンダライナー、圧延用ロール、鉄道車両用車輪など |
アルミニウム合金
鋳造方法 | 製品事例 |
---|---|
砂型鋳造法 | シリンダブロック、シリンダヘッド、ターボチャージャ用コンプレッサカバー、モータハウジング、モータプレート |
重力金型鋳造法 | ピストン、フライホイールハウジング、プーリー、インテークマニホールドなど |
低圧鋳造法 | シリンダヘッド、ホイール、ブレーキマスタシリンダなど |
高圧鋳造法 | ホイール、エンジンマウントブラケット、ステアリングラックなど他、コンプレッサー部品、油圧ポンプケーシング |
ダイカスト | シリンダブロック、トランスミッションケース、フォーターポンプケース、ピラーなどスクリュー、サブフレーム、高圧バルブ用リング |
マグネシウム合金
鋳造方法 | 製品事例 |
---|---|
砂型鋳造法 | ジェットエンジン、インレットケース、ベアリングサポート、ギヤボックス、モーターハウジング |
ダイカスト | シリンダブロック、オイルパン、クラッチカバー、ノートパソコンや携帯電話などの電気製などの筐体 |
銅合金
鋳造方法 | 製品事例 |
---|---|
砂型鋳造法 | 吸水栓用バルブ、排水金具、油圧・空圧用バルブ、海水ポンプ |
金型鋳造法 | メタルブッシュ、軸受、ウォームホイール、ギヤ、スクリューナット |
フルモールド鋳造法の工程は?
木村鋳造所のフルモールド鋳造法の製造工程を詳しく見てみましょう。
模型製作工程

鋳造工程

検査・加工・塗装工程

フルモールド鋳造法と木型法の違いは?
鋳鉄・鋳鋼で用いられる砂型鋳造法の中でも、特に「木型鋳造法」と「フルモールド鋳造法」を比較してみます。
フルモールド鋳造法と木型法の差
フルモールド鋳造法は『鋳型内の模型と溶湯を置換しながら鋳物を製造する鋳造方法』と定義することが出来ます。 すなわち、鋳型内を消失性模型で満たした状態で、この模型と溶湯を置き換えながら鋳造し、鋳物を作る方法です。鋳型内が、模型により満たされていることから、フルモールド鋳造法(Full mold casting)と呼ばれています。この呼び名は、木型法が空間の中に溶湯を注ぐ空洞鋳造法(Cavity mold )であるのに対して付けられたものです。図にフルモールド鋳造法と木型法の差を示します。
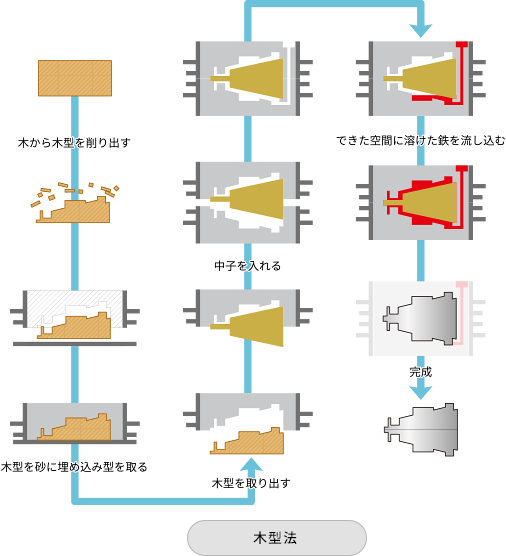
フルモールド鋳造法と木型法それぞれの利点
フルモールド鋳造法 | 木型法 |
---|---|
木型が必要ないので単品もしくは数の少ない物の納期が早く・コストが安い。試作品・単品鋳物・美術鋳物に向いている。 | 木型が繰り返して使えるため量産品に向いている。木型を作らなければならない問題がある。 |
製品と同じ模型を作ること、および発泡ポリスチレンの加工性が良いため、3次元ソリッドデータ及びCAD/CAMを簡単に利用できる。 | 木型は鋳物と逆の部分を作るために、また加工性が発泡ポリスチレンより悪いために3次元ソリッドデータ及びCAD/CAMを簡単に利用できない。 |
発泡ポリスチレンの燃え残り滓である、残渣が鋳物に残らないようにする鋳造技術が必要となる。このため、技術力のある鋳造メーカーでないとできない。 | 鋳型内が空間であるため、特別な鋳造技術を必要としない利点がある。このため、多くの鋳物メーカーで作ることが出来る。 |
木型の保管が必要ない。ソリッドデータを保管するだけでよい。 | 木型の保管およびメンテナンスが必要であり、木型管理費が必要である。 |
模型の段階で、設計上の問題点を確認することが出来る。また、模型の修正も簡単に行える。 | 木型法では、出来上がった鋳物を見て検査するしかない。また、木型の修正も簡単には行えない。 |
中子を必要としないため、造型時間が短く、複雑な鋳物が簡単にできる利点がある。また、設計上の制約も少なく、高度な技能も必要としない。 | 中子を必要とするため、設計上の制約が多く、複雑な鋳物を製作するには高度な技能を必要とする。中子作成の手間が掛かる。 |
抜き勾配が不要であり、設計上の制約も少ないことから、鋳物の軽量化が可能である。 | 木型法では、木型を抜くための抜き勾配が必要であり、設計上の制約も多い。 |
模型に複合材をセットするだけなので、複合材の製作等が容易に行える。 | 空間に複合材があるようにしなければ成らず、中子作業が複雑になることから、複合材の製作には不向きである。 |
フルモールド鋳造法の歴史
名称の由来
フルモールド鋳造法は、消失模型鋳造法・ロストフォーム・EPCプロセス・FMCプロセスなど種々の呼び名で呼ばれます。フルモールド鋳造法は、鋳型の中が空間である木型法のキャビティーモールドに対応した言葉です。
歴史
アメリカのシュロイヤー(H.F.Shroyer)によって出願されたフルモールド鋳造法の基本特許は、1958年に成立しています。1964年にはディーター(H.B.Dieter)とスミス(T.R.Smith)がドライサンド法による発明を、1967年にはドイツのヴィットモーザー(A.Wittmoser)とホフマン(Hoffmann)がマグネット法による発明をおこなっています。
フルモールド鋳造法の基本特許はドイツの断熱材製造会社であったGruenzweig & Hartmann社(略称G+H社)が実施権を1961年に取得し、同社の副社長に就任したアーヘン工科大学のヴィットモーザーがこの技術の工業化と世界への普及に尽力することになります。ヴィットモーザーはフルモールド鋳造法の育ての親と言うことになります。
日本では、三菱油化バーディッシュがヴィットモーザーの運営するフルモールドインターナショナルから特許の再実施権を 1965年頃取得し、三菱重工が技術開発を行うことになります。フルモールド鋳造法のファミリーは多いときには120社にものぼりました。当社も、 1966年11月にファミリーに参加しています。
当時のフルモールド鋳造法は、品質が悪くメリットが最大限に活かせるのは自動車用のプレス金型でしかありませんでした。 1993年11月フルモールド普及活動の中心となっていたヴィットモーザーが急逝したため、ライセンスグループ活動は終止符を打ち、各社独自で展開されることとなります。フルモールド鋳造法は、発泡ポリスチレンを製造する化学メーカーが、発泡ポリスチレンの商品拡大を目指す目的で行われることがわかります。ヴィットモーザーの唱えるトップ方案がよいか、当社社長の木村が唱えるボトム方案がよいか、世界を巻き込んだ議論が行われました。基本特許が消滅した1980年以降、それまでプレス金型のような大物鋳物が主体であったフルモールド鋳造法を、異形管や自動車部品等の小物に展開する流れがでてきます。
1980年にはジェネラルモーターがアルミ合金のシリンダーヘッドに、1982年にはフォードが、また1984年にはフィアットが小物量産品へのフルモールド技術の展開をおこなっています。これらの技術は、ノーバインダーの砂を用いて振動造型機で造型する手法が主体となります。この技術は、ロストフォームと言う呼び名が最も一般的です。日本でもほぼ同時期に、小物量産品へのフルモールド鋳造法の展開が行われており、第2次のフルモールドブームが起こることになります。
大物鋳物においては、フルモールド鋳造法の欠点である残渣(発泡ポリスチレンの燃え滓)の問題から、プレス金型以外への展開はなかなか進みませんでした。しかしながら、木型を必要としないフルモールド鋳造法は単品鋳物には最も適した鋳造法であることは間違いありません。当社は1974年から工作機械・産業機械へのフルモールド技術の展開を図ってきました。この技術を当社では、ニューフルモールド鋳造法(略してニューフル)と称しています。このニューフルの技術は木村特有の技術であったため、また単品物に限定したものであったため、ブームを引き起こすまでには至りませんでした。
1987年フルモールド模型をCAD/CAMを使って製作する方法が当社に導入されることになります。この技術により、量産鋳物への道が開かれることになります。フルモールド鋳造法による工作機械の量産品へのチャレンジが、木村鋳造所で行われることになります。この技術は、工作機械の複合鋳物そして産業機械へと進展していくことになります。
1987年に導入したフルモールド模型製作のためのCAD/CAMシステムは、その後の模型の作り方を根本的に変えることになります。従来は2次元の図面から空間を想像し、バンドソーなどを使って部品を作成し、これを組み立てて、模型を作成していました。コンピュータの発展と共に、手作りによる模型作りはCAD/CAMによる模型作りに変化していくことになります。当社においては、2002年に手作りゼロを達成することになります。この模型作りの大変革が、フルモールドの量産鋳物への道を開くことになります。
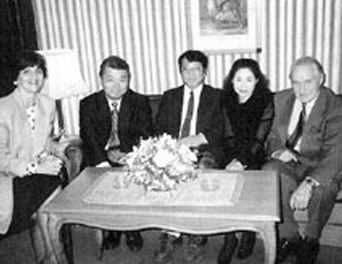
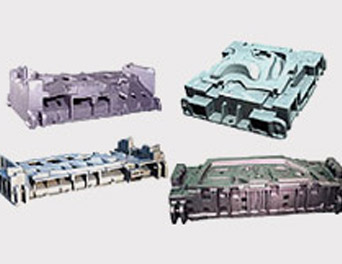
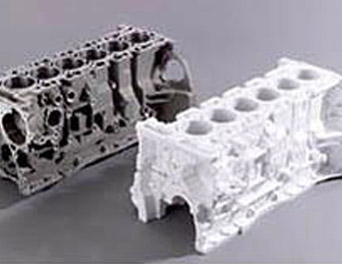